Basements
Building basements with ICF in the UK.
When properly executed, ICF Construction creates a high-quality, energy-efficient, and durable basement space for residential and commercial buildings.
Polysteel is the only UK ICF manufacturer with a BBA Certificate approving the forms suitability for use in basement construction (Section 4.4.).
Furthermore, the concrete forms a bond with our steel ties which stops water transmission through a wall. The larger polypropylene webs used in many ICF forms do not stop water transmission, because concrete does not stick to their large irregular profiles.
Basement Construction: 4 Main Steps.
Basements In Residential Buildings.
Basements in residential buildings can be of Grade 1, 2 or 3. Very few will fall into the Grade 2 category except for swimming pool halls and their plant rooms. The majority of projects will be Grade 3 for Residential use.
In residential buildings there are two typical structural layouts. Most dwellings have basements when the house is on a hillside and the rear wall is to be a retaining wall. The ground can slope down on either one or both sides of the building so the at the front of the house, the floor level is at the same level as the ground outside. In these circumstances it is relatively easy to ensure that water ingress does not occur by installing a land drain around the three sides of building that are retaining soil.
The alternative type of basement is where there is a whole floor level below ground. This requires more detailed consideration of the groundwater levels in the soil around the basement and the use of the basement.
Building Basements with ICF.
Our ICF PolyBloks are extremely useful and versatile in residential basement construction for the following reasons:
- They are a simple, fast way of building high quality retaining walls without the use of skilled labour.
- The high quality concrete core and the highly compressed EPS skins provide a structure that is virtually waterproof without additional measures.
- PolyBlok330s provide a safe retaining wall for most soils if the ICF basement is 3.5m deep (or less) below ground and the ground floor is used to prop the wall
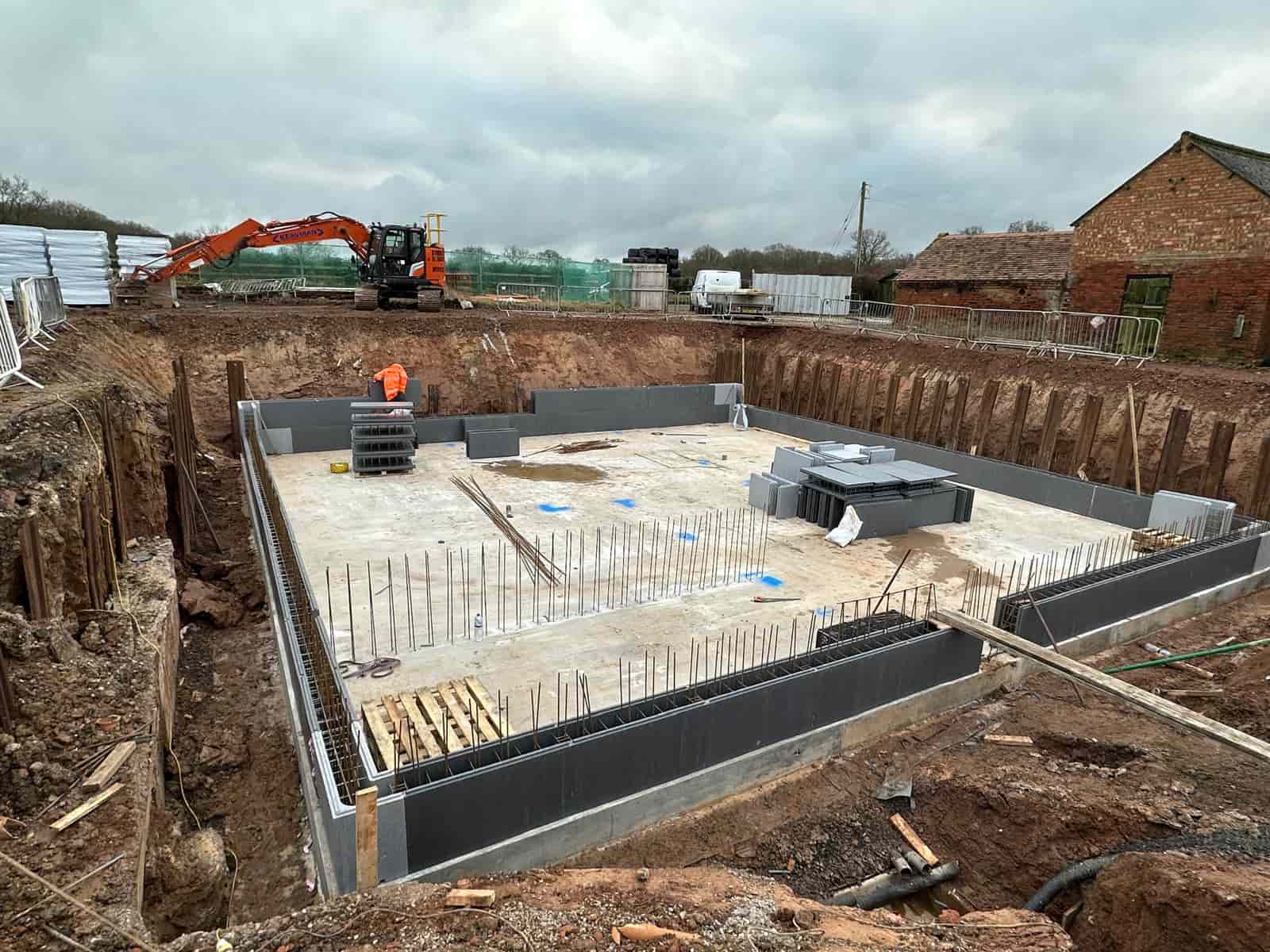
In virtually all soil types, DPM type membranes can be fixed to the outer wall and carried down the wall to enclose a perforated land drain at the foot of the wall. This can discharge into a soakaway, ditch or sewer on the slope below the house in most circumstances. However discharge into a sewer may require the consent of the local water authority.
If the ground water levels get very high it is possible to have leakage between the foot of the ICF PolyBlok wall and the base slab. In this instance, an internal drain can be provided around the perimeter of the building which drains to a sump with a submersible pump beneath the finished floor level in the basement.
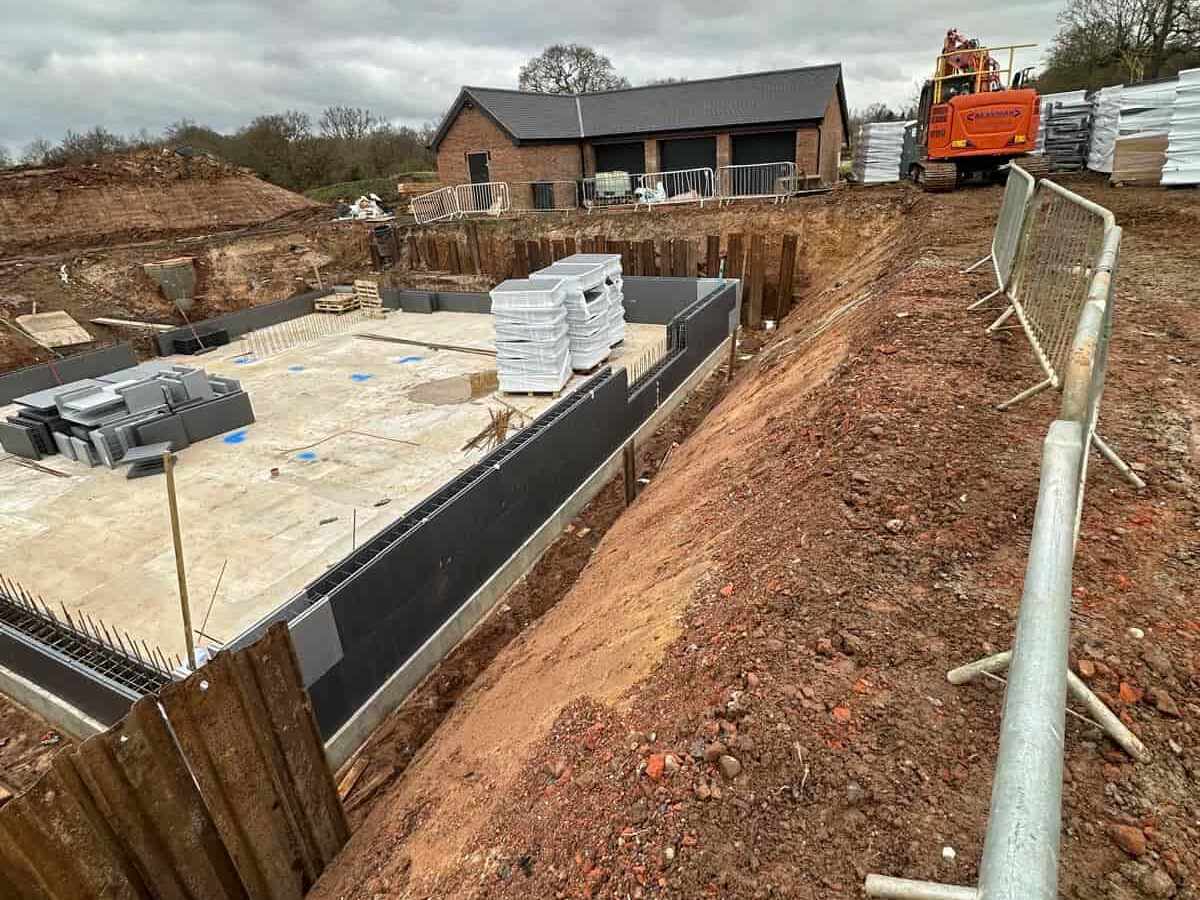
Basement Waterproofing Repairs.
Some websites claim ICF is unsuitable for basement construction because “They have a huge number of joints and the concrete cannot be checked after installation”. In fact, there is only one joint in an ICF wall and that is the one at the bottom of the wall between it and the base slab. The very high quality of concrete cured over weeks inside the EPS forms and the 3D grid of wires in ICF PolyBloks stop all shrinkage cracks. As a result, ICF PolyBlok walls are virtually waterproof without specialist waterproofing and are far superior to concrete walls built with formwork. However, it is essential to ensure the concrete pour is carefully controlled to ensure that the correct specification is used and the concrete is vibrated properly.
ICF basement leaks might be difficult to repair but they will not leak if they are designed and built properly in the first place.
If there are any doubts about the likelihood of persistent high water levels in the ground around the basement then an internal drain should be installed as shown in the Type 1 sketch below.
Structural Options.
There are two primary structural arrangements incorporating the use of Polybloks in an ICF basement retaining wall:
Type 1:
Inverted T type retaining walls are built with the toe of the wall about 400-500mm below the internal floor level. The floor is then formed in a conventional beam and block type floor. Supported by concrete block sleeper walls that are built on the toe of the retaining wall at one end and conventional footings at the other end. This is mostly used on hillside buildings where the front of the building does not need to be a retaining wall or where there is a risk of water penetration.
Type 2:
The entire basement floor is covered by a reinforced concrete floor slab that can be 200-300mm deep, depending on the width of the basement. The ICF walls are then installed around the starter bars that are cast into the basement slab. Further reinforcement is installed over the entire wall so the retaining wall and basement slab act as one structural element.
Considerations.
Reinforcement that has a diameter greater than 12mm is very difficult to use in ICF. The horizontal steel bars must be specified in a way that suits the ICF course heights. Many Structural Engineers over provide the area of steel required because of their ultra-conservative approach to retaining wall design.
In most basements less than 3m high, vertical reinforcement should be no more than H10 bars at 150mm c/c if the wall is propped by the ground floor before backfilling around the basement walls.